60 Years of Precast
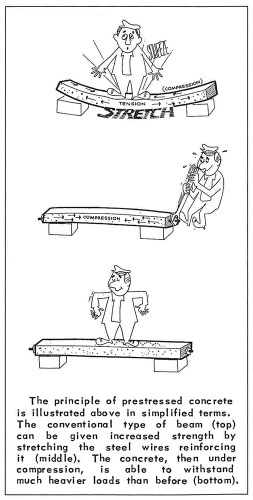
In post-World War II suburbia, the housing boom of the era meant young families needed more than just residences. An entirely new suburban infrastructure was required, and considering the educational, social, and religious needs in communities, that meant schools, community centers, and places of worship. It would also need to include shopping centers and supermarkets, office buildings and industrial plants, and of course: roads to support the federal government’s massive national interstate highway system.
To meet demands while keeping costs down, contractors, engineers, and architects stressed the need for speed, economy, and efficient construction as opposed to complex or unique architectural styles that had been popular in the past. The best thing for speed would be a mass production of standardized building components that could be used for quick on-site assembly. One thing was certain: ornate design was out and economy was in.
Engineers quickly solved the problem by adapting a new technology for concrete: prestressing it to create the simple modular panels, planks, and beams needed for long-span floors, roofs, and bridges. Under controlled factory conditions, plants could mass-produce these modular components to standardized specifications, making it far easier to meet increasing demand for building materials.
Quite suddenly, buildings and structures of all kinds – including hotels, shopping centers, stadiums, and schools – began incorporating prestressed concrete products into their designs. While prestressed concrete is often visible, it often goes unrecognized despite becoming a key structural material in buildings of all types during this time.
From Europe to America
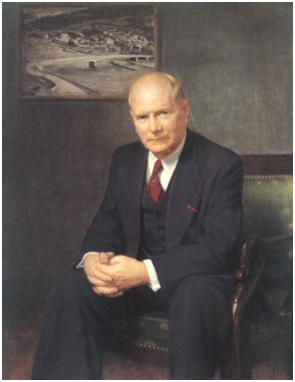
It was French bridge engineer Eugene Freyssinet who championed the theory and use of prestressed concrete in the 1900s by combining the tensioned strands of high-strength steel with high-strength concrete to create a prestressed concrete able to withstand a much greater tension without cracking or permanently bending. Belgian engineering professor Gustave Magnel, however, was the one who broadened the appeal of prestressed concrete by demonstrating how it was simultaneously stronger and more economical than reinforced concrete. In fact, through Magnel’s own student, Charles Zollman, Magnel helped design the Walnut Lane Bridge in Philidelphia, which famously became the first prestressed-concrete beam bridge built in the United States in 1950.
Even though Magnel said in 1954 that mass production of prestressed-concrete bridge components was unlikely or even impossible – based primarily on his European experience of highly customized projects – U.S. manufacturers soon proved otherwise. Contractors, engineers, and architects, faced with meeting huge post-World War II demand for buildings and other infrastructure, welcomed the new product with the standardization of prestressed units.
More Than Bridges
Although the original experimentation and testing of prestressed concrete focused mainly on bridges and bridge beams, the material soon found other places in the new and expanding suburban world. Beginning in the 1950s and expanding in the 1960s and beyond, a wide array of new buildings going up in the suburban landscape were using prestressed concrete for major structural components.
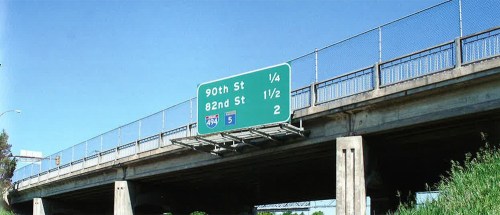
Prestressed Concrete, Inc. (PCI), who fabricated the beams used in the first major prestressed-concrete bridge on a Minnesota state highway (Bridge 9053), was servicing Minnesota, North and South Dakota, Iowa, and western Wisconsin out of their Roseville plant. They offered prestressed channel slabs for floors and roofs, prestressed girders, and prestressed bridge members, along with precast columns, walls, manholes, and custom products. Their first non-bridge projects included Westwood, a small shopping center in St. Louis Park, and a high school sports stadium in Bloomington. The latter was eventually part of the Bloomington High School construction project that produced the first prestressed, precast-concrete stadium grandstand in the Twin Cities. PCI pushed advertising that emphasized their precasting abilities “under ideal factory control,” promoting the advantages of manufacturing off-site year round.
Late in the 1950s, Paul and Bill Radichel of Mankato created Spancrete Midwest Company, setting up a plant in Osseo (or Maple Grove, as the successor company identified its location today) using a version of the German machine for hollowcore reworked by Henry Nagy. Spancrete established the first use of hollowcore slabs in the U.S. in 1954, and by 1960, the Radichels began operating Spancrete Midwest’s 600-foot casting bed. The new Osseo plant stood alone in a future suburban industrial park. In St. Paul, Molin Concrete Products Company, established in 1905, decided to dive into the prestressed-concrete business around the same time. They, in contrast, were using the Flexicore Hollowcore manufacturing process in their plants
History of Prestress Concrete – The First Fifty Years Video
Enter Wells Concrete
Wells Concrete Company in Wells was established in 1951 by Frank Balcerzak, who had owned the Guaranteed Gravel and Sand Company of Mankato. Instead of focusing on producing bridge beams, he instead turned his attention to the new prestressed “double-tee” beam and finally began Wells’ prestressing operation in 1957 with help from a Florida consulting firm specializing in prestressed concrete. Leo Nesius was the first hire, and would hold the position of Vice President and General Manager until Balcerzak’s passing in 1970, after which he would take over as President.
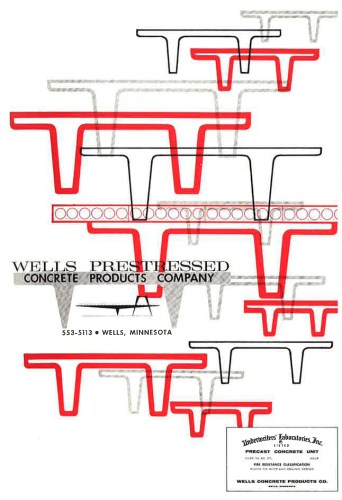
This new form quickly became a primary structural member in the industry, useful for longer spans where hollowcore slabs were too short or too light. Wells recommended its slabs for schools, chur ches, factories, warehouses, and stores, and promoted the double-tee for shopping centers, supermarkets, and dormitories.
An advertisement in 1962 noted the double-tee’s fire-retardant rating and fire safety became a high selling point for prestressed concrete building components. Architects developed aesthetic interest by revealing certain parts of the double-tee beam, transforming the functional tee-stems into linear exterior features and exposing the ends for a repetitive roofline or cornice detail.
By the middle of the 1960s, the prestressed-concrete industry had established itself in Minnesota, and the firms that would dominate the state’s industry for subsequent decades were up and running. David Billington, who had also studied under Professor Magnel, called prestressing “the single most significant new direction in structural engineering of any period in history. …Moreover, the idea of prestressing opened up new possibilities for form and aesthetics.”
Indeed, few Minnesotans realized they were surrounded by a radically new technology. They were studying in prestressed concrete schools, worshipping in prestressed concrete churches, and shopping in prestressed concrete malls. They were parking in prestressed-concrete ramps and driving under prestressed-concrete bridges. Prestressed concrete had transformed the world in the decades after World War II, and continues today as a widely used building material, with even more forms and shapes added in subsequent decades. The technology behind it is central to nationally recognized Twin Cities landmarks spanning more than half a century: The Metropolitan Sports Center in Bloomington, the Minnesota Timberwolves Arena, and the parking ramps at the Mall of America, the largest in the world when they were built in 1992.